June 07, 2024
College Park, Md. (Highpoint Digest) — Engineers at the University of Maryland (UMD) have developed a model that combines machine learning and collaborative robotics to overcome challenges in the design of materials used in wearable green tech.
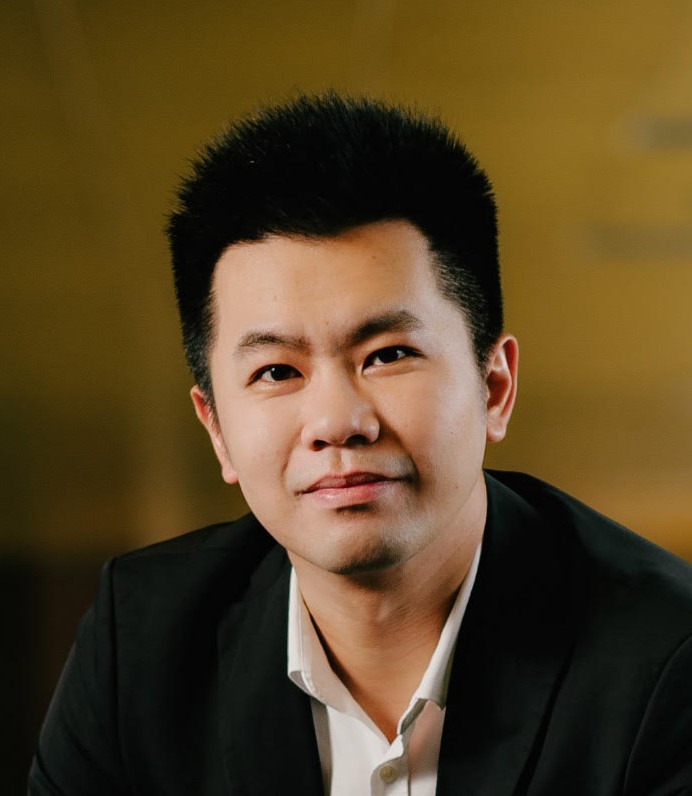
Led by Po-Yen Chen, assistant professor in UMD’s Department of Chemical and Biomolecular Engineering, the accelerated method to create aerogel materials used in wearable heating applications – published June 1 in the journal Nature Communications – could automate design processes for new materials.
Similar to water-based gels, but instead made using air, aerogels are lightweight and porous materials used in thermal insulation and wearable technologies, due to their mechanical strength and flexibility. But despite their seemingly simplistic nature, the aerogel assembly line is complex; researchers rely on time-intensive experiments and experience-based approaches to explore a vast design space and design the materials.
To overcome these challenges, the research team combined robotics, machine learning algorithms, and materials science expertise to enable the accelerated design of aerogels with programmable mechanical and electrical properties. Their prediction model is built to generate sustainable products with a 95 percent accuracy rate.
“Materials science engineers often struggle to adopt machine learning design due to the scarcity of high-quality experimental data. Our workflow, which combines robotics and machine learning, not only enhances data quality and collection rates, but also assists researchers in navigating the complex design space,” said Chen.
The team’s strong and flexible aerogels were made using conductive titanium nanosheets, as well as naturally occurring components such as cellulose (an organic compound found in plant cells) and gelatin (a collagen-derived protein found in animal tissue and bones).
The team says their tool can also be expanded to meet other applications in aerogel design – such as green technologies used in oil spill cleanup, sustainable energy storage, and thermal energy products like insulating windows.
“The blending of these approaches is putting us at the frontier of materials design with tailorable complex properties. We foresee leveraging this new scaleup production platform to design aerogels with unique mechanical, thermal, and electrical properties for harsh working environments,” said Eleonora Tubaldi, an assistant professor in mechanical engineering and collaborator in the study.
Looking ahead, Chen’s group will conduct studies to understand the microstructures responsible for aerogel flexibility and strength properties. His work has been supported by a UMD Grand Challenges Team Project Grant for the programmable design of natural plastic substitutes, jointly awarded to UMD Mechanical Engineering Professor Teng Li.
Source: University of Maryland
Images courtesy of the University of Maryland